Generalities
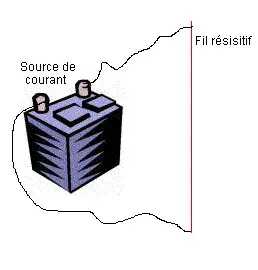
The principle is quite simple, there is a strong electric current in a thin resistive wire. The wire under the effect of current, heat and cut easily and cleanly styrofoam, much much better than with a knife or a cutter, particularly for large pieces (> 5 cm thick).
It can also be use to cut plastic or synthetic foam.
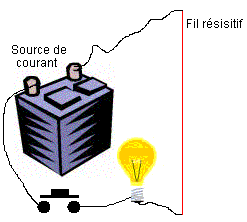
Build a filicutter is only adding a current source to resistive electrical wire, adding a control switch and possibly a light bulb to limit a bit the current passing through the wires.
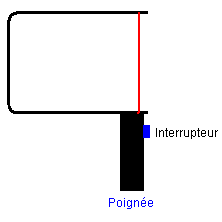
And of course mount the whole on a structure, insulated, easy to handle, so you can control the hot wire during phases of cut. The idea was to do something that looks like a bit to a saw wire, a kind of huge "U" who owns a handful at the end.
This way you control switching on/off heater wire with a finger, and guide cutting with the same hand.
What you need
- Resistive wire: not easy to find, you can try electronic components dealers, hardware, paint stores or plastic arts shops. This wire (sometimes called "constantan"), can also be replaced by piano chord/wire but's it is more fragile. Other idea by Alain, the recovery of resistance in an old radiator or electric toaster, you may need to increase or decrease the energy voltage depending on what you want to obtain (see below)
- A piece of plastic pipe: to do the handle, take about 10 cm or 4 inches of plastic plumbing pipe
- A push-button: for switching on (electronic components dealers)
- A piece of metalic pipe of 1 cm diameter: To make the "U", at your size. Mine is 26x30 cm or 10X12 inches, made from an old aluminium tent pole
- Electric wire: To put electric power to heating wire throught push-button. Take any kind of wire, with two sub-wires, and not too thin (bigger than telephone or network wires)
- A power source: One more time, anything you can get who could deliver a 20 volts power, no matter AC or DC (I use an old car battery chargeur)
- Miscellanous: Electrical scotch-tape, some bolt and nuts
How to
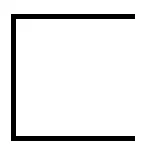
Fold metalic pipe to make the "U" according to your dimensions.
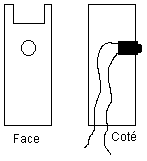
Cut the handle in plastic pipe. On top of this pipe, make (using a saw) a place for the "U". Make a hole for your push-button, in the right place for your finger as a trigger. Connect two wires to push-button, and put them inside the handle.
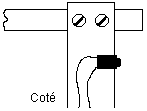
Put the "U" in the handle, let 2 cm - 1 inch exceed, and fix it by making two holes througt the handle. Put two bolts in those holes, and put two nuts on the other side. You should have in your hand something light, with push-boutton right under your index.
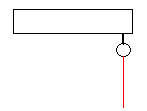
Add then the resistive wire on the "U". On top, use a small metallic bolt with a ring head. You shoud use metallic bolt because and electric contact is needed on that side.
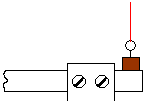
On bottom, contrarily wire should be insulate from the "U": use a small piece of wood, fixed with another bolt and nut, then another metallic bolt with a ring head.
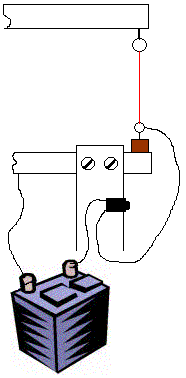
Then connect:
- One arrival of power to the "U" (using an alligator clip for example).
- The other power arrival on one probe of the push-buttonl
- The second probe of push-button to the bottom metallic bolt with a ring head
Alain told me that you should be careful with styrofoam smokes when cutting, they are toxic and should not be breath.
Evolutions
Filicutter with handle like this one is very useful for... sculpturing styrofoam, but it's a bit difficult to make straight cuts.
If you have this kind of cuts to do, it could be interesting to improve it by making a kind of stand. The idea is to make this stand with a right-angle system and another push-button commanded by your feet, so that your two hands are free to control the styrofoam piece move.
To do that, you should make a small table, with a hole in and where the wire pass through. Table and filicutter should be in right angle, stable and connected, for example in a clamp.
Home made filicutter
Here is some photos of mine (click to enlarge) :
Conclusion
You could now, according to your needs, enhance the filicutter. Just in case, here is some lines of enquiry:- Using a lamp to enlighten the place where wire cut (more comfortable).
- Adding a guide for cutting on a side, to be sure to have straight cutted pieces.
- Adding a regulation sytem for bending wire, no matter it is cold or hot.
- Etc...
Of course, if you want to give or ask precisions or informations, don't hesitate to contact me.
The 43 comments already posted on this page
I use 12 v car battery and for wire i use continuous welding wire heavy gauge for fabrication
You will have to tighten wire when it heatsup
It cuts all my sheets of insulation 1 in 2 in 3 ect...
You will need to practice but it works
For the battery wire use standard cooper wire of appropriate diameter (not too small).
It's just for science project.
But you'll certainly need to push the piece of foam a bit slower, to get a nice cut.
Anyway no need to be precise, any wire will be ok.